6 control methods of air compressor
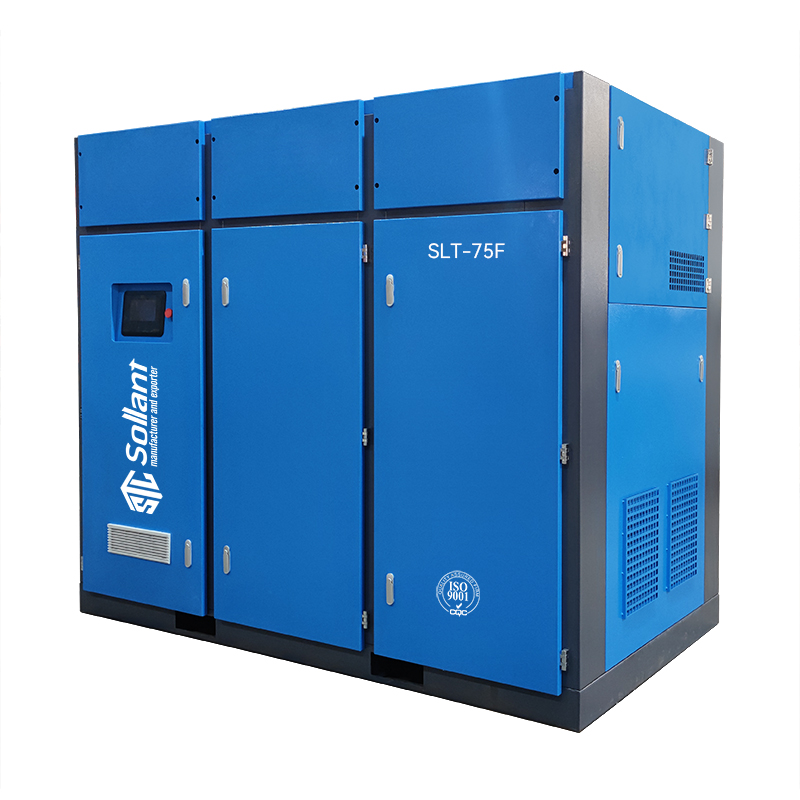
The goal of the air compressor control system is to match the demand and supply of compressed air most efficiently. Although some control methods have been eliminated with technological advancement, basically all control systems can be divided into two major categories, namely fixed speed control and Variable speed control.
1. Fixed speed control
As the name suggests, this method is to keep the air compressor speed constant. The specific speed is determined by the drive motor speed and the transmission ratio function of the transmission device. The transmission device can be a gear or a V-belt port, while the air volume control is based on modulation control or poppet valve control.
2. Variable speed control
Variable frequency drive variable speed control is the latest technological achievement application of air compressors. The principle seems simple, that is, to accurately control the speed of the air compressor/motor according to system requirements. If designed properly, variable frequency control is the most advanced and energy-saving control interface for air conditioning compressors. However, some of the following problems must be solved. The air compressor main engine must be designed to have high efficiency in the entire speed range. The main engine efficiency is a function of the linear speed of the rotor tooth top, and may drop significantly when the speed is too low or too high. The variable speed drive controller acts as an additional link between the power source and the drive motor and must be efficient. The drive system and motor performance must be free from power distortion and electromagnetic radiation to prevent computers or other sensitive electronic equipment from receiving electromagnetic interference. Drive motors must handle high speeds as efficiently as low speeds, where bearing design and cooling issues can be troublesome. The intelligent controller establishes an efficient and reliable connection between air pressure, electric motor and air compressor intake valve. A well-designed device can accurately control compressor discharge pressure to within 1 Psi, despite wide fluctuations in air demand. Variable speed control is suitable for adjusting the operation of multiple air compressors. It allows the sequencer/controller to operate efficiently in parallel air compressors. Some air compressors can operate at full load according to demand, while the remaining air compressors are on standby. Variable speed control can Effectively compensate for the fluctuation of gas demand.
3. Modulation control
This form of control adjusts the air compressor’s intake valve based on the air compressor’s exhaust pressure. When the controller detects that the exhaust pressure has increased, it begins to close the intake valve. Although this control is effective, it is minimally efficient. The reason is that the efficiency of an air compressor is inversely proportional to the pressure ratio, which is the ratio of exhaust pressure to intake pressure. The closed intake valve creates a vacuum at the inlet of the air compressor, while the exhaust pressure remains relatively unchanged, which is equivalent to increasing the pressure ratio. The remedy is to limit the adjustment range of the modulation control to approximately 40%, and automatically convert the control scheme to load/no-load control once the output drops below 60%. Unfortunately, this control cannot be applied to multiple machines.
4. Variable discharge control
Controlling the effective rotor length can change the air compressor displacement. This is mainly achieved by adding a poppet valve or spiral valve to the main engine to control the internal bypass. Although the efficiency of this control is better than modulation control, spiral valve control is only effective above 50% to 60% capacity, and the debugging of this control is complicated and difficult.
5. Offload control
This control is simple and effective. It uses the pressure rise and shutoff at the exhaust of the air compressor to completely close the intake valve when the upper limit (disconnection) pressure is reached, and completely open the intake valve when the lower limit (connection) pressure is reached. The difference from modulation control is that the air compressor under this control implements internal unloading. The decrease in pressure ratio leads to a decrease in wasted power consumption. This type of control can easily connect multiple air compressor devices using a sequencer (master) controller. Air systems, on the other hand, require the installation of a properly sized air storage tank.
6.Switch control
This is the most effective control scheme. The air compressor either runs at full load or stops, depending on the signal port at the pressure switch. However, if a motor exceeding 10hp is frequently started and shut down according to the requirements of this control, it will cause overheating. This type of control is often used on small piston air compressors equipped with a reservoir. The pressure difference of this type of air compressor is relatively large, reaching 15 psig to 25 psig.