Analysis of Construction Status of Compressor Station | Analysis of Operation Status
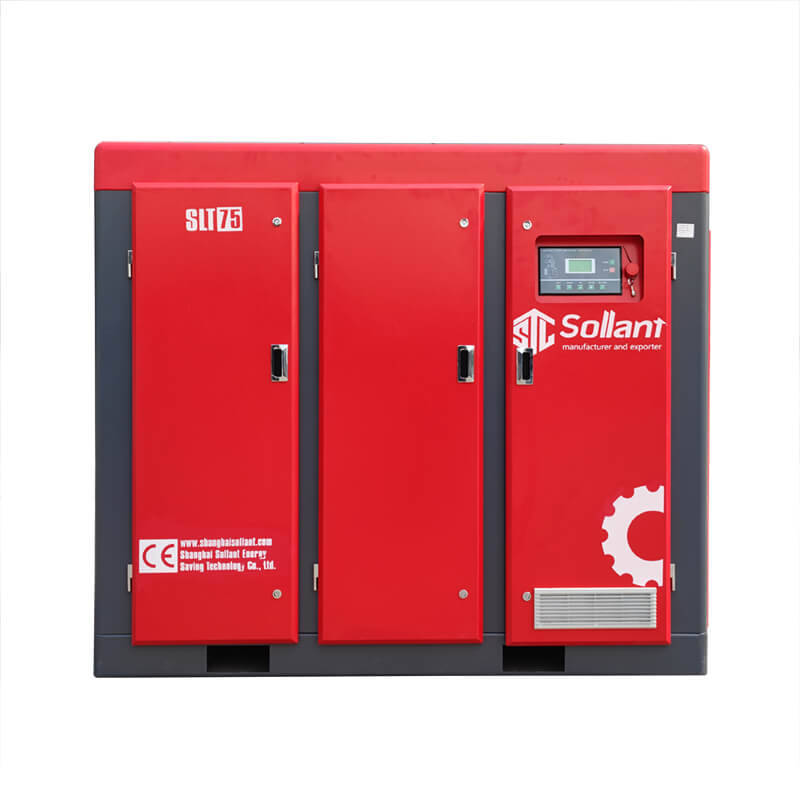
Analysis on Construction Status of Compressor Station
The construction of a compressor station is a complex system engineering, from feasibility study, demonstration, planning, design, construction to final acceptance and commissioning, all of which consume a lot of materials and labor. The construction of a compressor station equipped with ГТК-10 gas turbines in the former Soviet Union required more than 6,000 tons of steel and 170,000 man-days. Considering that most of the compressor stations must be built in uninhabited areas and inaccessible areas with harsh natural conditions, Soviet builders adopted industrialized construction methods to speed up construction. All compressor stations adopted a standardized design and used a large number of standard prefabricated concrete modules and prefabricated steel structure modules. Facts have proved that through scientific planning and management, the progress of pipeline construction can be greatly accelerated. Among them, the most notable Urengoy-Central Line 1 pipeline with a length of 3,022 kilometers was put into operation in only 10 months, 53% shorter than the plan.
At present, the domestic demand for natural gas consumption is increasing rapidly, and the construction of natural gas pipelines and compressor stations is also in progress. Learning from foreign pipeline construction experience can formulate reasonable plans and plans to achieve the purpose of rational allocation of resources. The construction of domestic natural gas pipelines draws lessons from foreign experience to a certain extent, but due to the limitations of the domestic basic industry level, both the construction and operation of pipelines and affiliated compressor stations still need to be further improved in many aspects.
Take the safety renovation project of a certain compressor station of the West-East Gas Pipeline as an example: the pipeline starts from Xinjiang in the west, passes through more than ten provinces and cities, and arrives in Shanghai. Continuously increasing, the demand for gas supply is increasing year by year, and it is imperative to improve the transmission volume and the reliability of stable and efficient gas supply of pipelines. In the early stage of construction, imported complete sets of combustion-driven centrifugal compressor units were adopted in places with relatively difficult natural conditions in the western section. Since 2010, some compressor stations in the western section have added a compressor unit of the same type to the original configuration, replacing the original 1 +1 run mode becomes 2+1 run.
Due to the tight construction schedule of the renovation project and the use of imported equipment, the first cooperation between the domestic construction contractor and foreign equipment suppliers, there are certain differences in construction technology, resulting in multiple failures during the equipment installation and trial operation. like
(1) Fuel gas leakage caused by the fastening method of pipeline connectors not meeting the requirements;
(2) The oil in the gas turbine box was not cleaned up in time, and the high temperature generated during the operation of the equipment caused the oil to volatilize, causing the fire protection system to be triggered by mistake;
(3) The suction and sweep quality of some pipelines in the sealing system is not up to standard, causing a large amount of dirt to block and damage the precision filter, resulting in the scrapping of parts, and a series of problems that cause delays in the construction period.
In addition, problems in the organization and coordination of the work plan were also exposed during the construction of the renovation project.
(1) The construction schedule was not strictly enforced in the early stage, and the construction quality declined when the ignition date was determined to catch up with the schedule in the later stage;
(2) The foreign suppliers realize the control of the work progress through strict work flow and technical means, comparatively speaking, it is difficult for the technical personnel of the owner to play an actual coordination role, and there are defects in the management of the suppliers;
(3) The environment was severely damaged during the construction process, and civil construction waste and industrial waste were not disposed of in accordance with regulations, causing certain damage to the site environment.
Analysis of the Operation Status of the Compressor Station
The main function of the compressor station is to pressurize the natural gas in the pipeline. Usually, the compressor station uses multiple centrifugal pipeline compressors to operate in parallel to ensure that the gas turbine can provide sufficient power under the worst weather conditions. In addition to the compressor unit installed in the common compressor station, a series of gas filtration devices and various complete sets of auxiliary equipment to ensure the normal operation of the compressor unit are usually installed. In recent years, due to the limitation of the energy utilization rate of the gas turbine itself, some advanced compressor stations have begun to install residual energy recovery devices to recover part of the available heat energy from the high-temperature flue gas emitted by the gas turbine for power generation and heating. No matter how the configuration of the compressor station changes, the core issue for pipeline operation is mainly high reliability. Generally speaking, high reliability is mainly achieved through the following two ways:
(1) Adopt more reliable equipment and make reasonable configuration;
(2) Adopt advanced maintenance concepts, formulate scientific maintenance plans, and ensure that the equipment is in good condition.
Based on the analysis of the operation data of the compressor stations of the West-to-East Gas Pipeline in the past 10 years, the first six months to one year of operation of the compressor stations is a period of high incidence of failures. This conclusion is in line with the principle of “bathtub curve”. From previous statistical data, it can be seen that the cascading shutdown triggered by field instrument failure is one of the important reasons for the high incidence of failures in the early stage of operation. In addition, the IO card and controller failure of the control system is also an important factor triggering the cascading shutdown.
In addition to the above internal reasons, external factors will also affect the operation of the compressor unit. Since the operation of gas turbines relies heavily on air and requires high air quality, in order to protect gas turbines, an interlock protection system is usually used to monitor important parameters of the air and the environment in real time, and once it finds that it is unfavorable to the equipment, it will automatically stop the operation of the unit. In fact, since long-distance natural gas pipelines often span thousands of kilometers, and the climate and natural environment are complex and changeable, if all compressor stations along the line adopt the same protection parameters, over-protection may occur. According to statistics, there have been many unplanned shutdowns of compressor stations caused by strong winds, rain, fog, and sand and dust. What’s more, heavy fog has caused compressor stations to fail to start compressor units for more than 24 consecutive hours, causing serious damage to gas transmission. Serious impact.
In conclusion
In recent years, the speed and scale of domestic natural gas pipeline construction have been increasing, but there are still many problems compared with foreign advanced levels, mainly in the following areas:
(1) Constrained by industrial level and design concept, the construction and operation of most natural gas pipelines and compressor stations in China cannot fully reach the modern industrial level of standardization and modularization;
(2) A large number of core equipment of the compressor station still needs to be imported, and independent production cannot be realized. However, foreign suppliers have insufficient understanding of the actual situation in China, resulting in poor adaptability of the equipment, which greatly increases the construction and operation costs of the compressor station.
(3)With the construction of long-distance natural gas pipelines, the level of domestic industry is gradually improving, and the concept of industrial design is gradually improving. Problems in the construction and operation of natural gas pipelines and compressor stations played a role.
Sollant Group-Professional Compressed Gas Solutions Provider