Excessive air compressor vibration? These 5 points may be the culprit
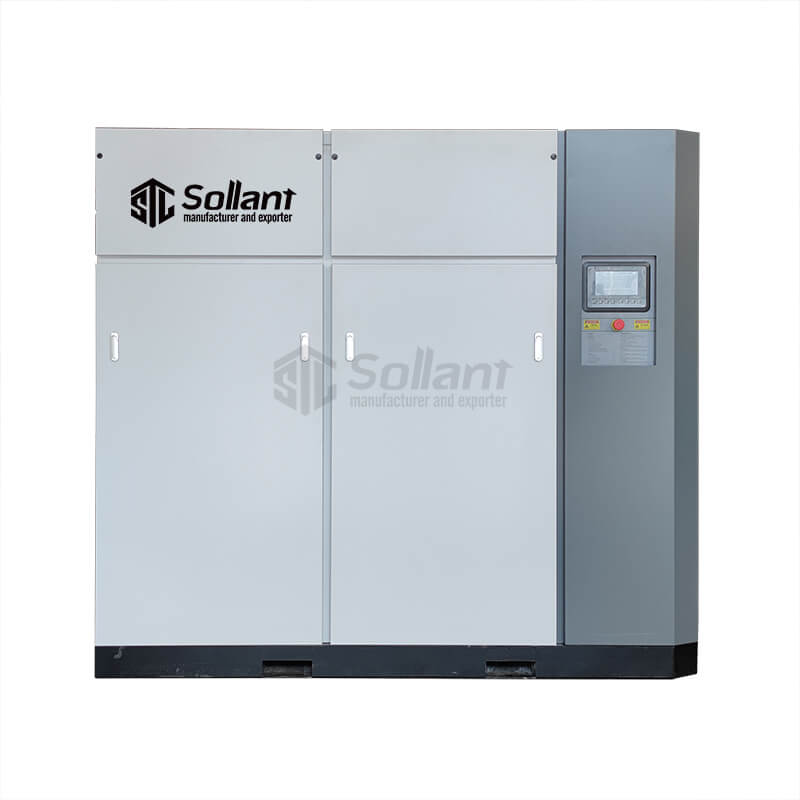
01. Vibration after driving
When the unit is started, due to the large starting current of the unit, the instantaneous torque is also very large, causing the motor to have a sense of displacement, and in the process of starting, it is an unstable process to pass through the surge region, and the vibration fluctuates obviously.
Take an air compressor of a certain company as an example. Because the start-up is not standardized, the position of the inlet guide vane and the scale are often inconsistent when starting up. As a result, when starting up, the starting current is very large, and it is even obvious that there is a surge phenomenon, resulting in very large vibration after starting up. Therefore, the service life of the compressor is affected by repeated start-ups, and frequent shutdowns are required for maintenance.
Frequent starting and stopping will also affect the vibration of the unit. Due to the influence of considerable conditions or mechanical failure, it is forced to start and stop many times a year, which destroys the balance of the rotor. When parking, the dust or other oxides accumulated on the rotor will fall off unevenly, which will destroy the balance of the rotor.
Due to the large torque at the moment of starting and stopping, the impact and wear on the gear shaft and the seal are great. Although the seal and the shaft fit within the acceptable range, there will be a large axial displacement, which will always cause wear to a certain point of the seal and the shaft. Destruction, the surface smoothness of the seal or shaft will be reduced, which will increase the vibration and even damage the equipment.
02. Impact of bearing bush
In the past, air compressors often used two tiles for sliding bearings. After 2003, the sliding bearings of air compressors were modified, and the bearing bushes were upgraded on the basis of the original air compressor body. The amount of oil between the pad and the shaft has increased, although the lubrication and cooling performance has improved, the sealing performance is not as good as the original sliding bearing; but the vibration has been reduced, and the mechanical efficiency has also been greatly improved, which has been recognized by the industry.
The defect is that the bearing temperature and vibration detection equipment often drift and jump, and the readjustment is only based on experience and lacks standards, which makes the daily monitoring fail and brings misjudgment to the operator.
03. The influence of condensed water
Condensed water with corrosive gases in the air causes severe corrosion of rotors, air seals, diffusers and carbon steel air pipes, and generates air vortex vibrations. The scouring of pipeline oxides caused the balance of the rotor to be damaged, and the vibration was violent, so it was forced to stop. Such accidents have occurred twice.
The influence of condensed water, especially in humid weather, the condensed water is not discharged in time, or the steam trap is faulty, so that the condensed water cannot be discharged, so that the water is brought into the impeller. Increase the vibration and damage the equipment.
04. Poor alignment, axial displacement causes vibration value to increase
Couplings are used to transmit motion and torque between the cylinders. Due to the installation error of the unit, thermal expansion under working conditions, deformation after loading, and uneven settlement of the unit foundation, etc., it is possible to cause a gap between the axes of the cylinders when the unit is working. Misalignment. Misalignment will cause alternating forces in the axial and radial directions, causing axial vibration and radial vibration, and will increase as the severity of the misalignment increases.
There are errors in the installation of the coupling, unbalanced manufacturing of the coupling, excessive deviation of the end face of the coupling, insufficient manufacturing accuracy of the elastic coupling, and unequal cancellations will cause the failure of the coupling. The main causes of bearing defects are the large gap between the bearing pads and the whirl of the oil film.
In addition, the axial displacement will also increase the vibration of the vehicle. Taking a faulty compressor as an example, the coaxiality of the motor and the large gear was completely corrected according to the design requirements during installation. Installed according to the design requirements, the radial and axial errors are generally allowed within 0.02mm.
After the unit has been running for a period of time, it is measured that the axial direction has changed, and the horizontal direction of the radial direction has obviously moved by about 0.18~0.20mm. This shows that the vibration will be very large when the machine is running after being centered.
05. Insufficient gear contact surface
Insufficient contact of gears causes power frequency vibration caused by unbalanced load of gears. The speed of the turbine is very high. Taking a compressor as an example, the speed of the 1st and 2nd stages is 15200r/min, so the precision requirements of the gears are also very high. It is very important to maintain a high gear contact surface. Checking the gear contact surface under static conditions cannot obtain the actual dynamic contact situation. Our method is static to make the contact surface not less than 85%.
One of the units found that the gear contact surface was poor during maintenance, and a new gear was severely pitted and peeled off after only two months of operation (the current price of a large tooth is 300,000). The vibration of the unit is very large, and the damage of the gears is a vicious circle, which is difficult to save.
The static balance and dynamic balance of the rotor caused by rotor manufacturing errors, assembly errors, and uneven materials, etc., will cause vibration at the beginning of trial operation; after long-term operation, the rotor will be caused by imbalance Rotor unbalance caused by uniform fouling, uneven deposition of dust in the medium, uneven wear of blades and impellers by particles in the medium, etc., shows that the vibration value gradually increases with the prolongation of the running time; The rotor is unbalanced due to the falling off of parts or the adhesion of foreign matter in the flow channel of the impeller, and the jamming, which is manifested by a sudden increase in the vibration value.
Sollant Group-Professional Compressed Gas Solutions Provider