The secret of permanent magnet material in frequency conversion screw machine
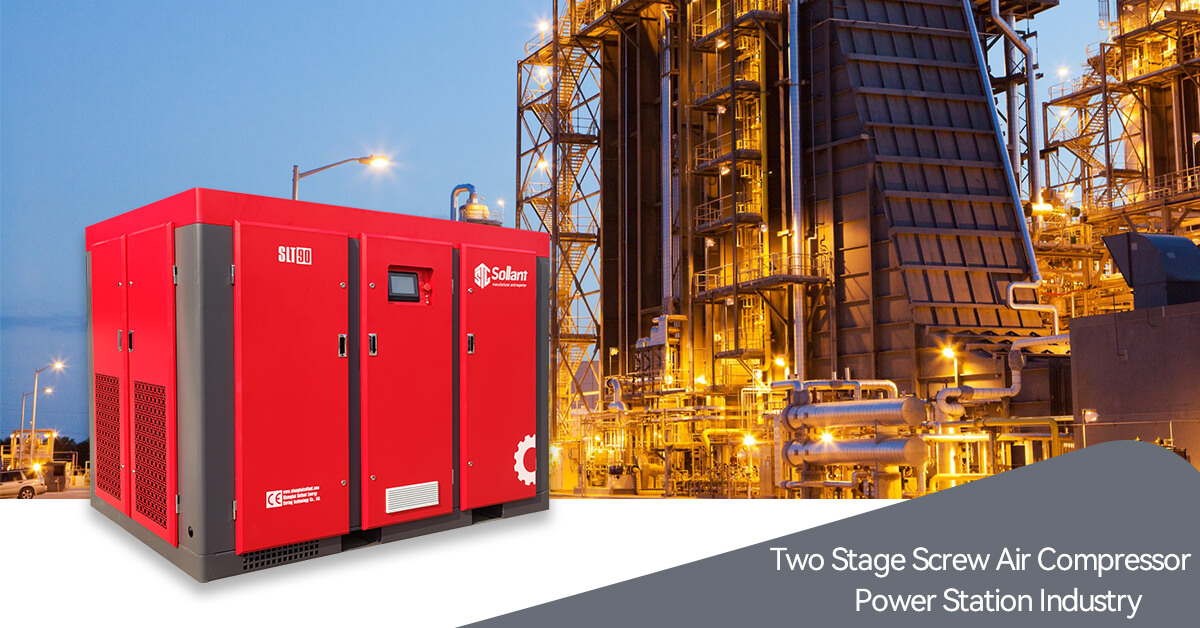
The permanent magnet frequency conversion screw air compressor is a permanent magnet motor made of rare earth permanent magnet materials. The rotor realizes rare earth permanent magnetization, no slip, no excitation, no fundamental wave iron and copper loss in the rotor, and less heat generation, which reduces the stator load. Losses in current and stator resistance. Its efficiency is 5%~12% higher than that of asynchronous motors with the same capacity.
3 advantages:
1. Save the loss when the screw machine is unloaded
When the gas consumption of the screw machine fluctuates, 45% of the electricity will be consumed when the motor is unloaded; the permanent magnet variable frequency screw machine has no unloading, and there is no waste. The more the system, the more energy saving.
2. Save the loss of the pressure difference of the screw machine
In order to avoid the impact of frequent start-up on the unit and the power grid, the screw machine is set with a pressure difference of 1-2 bar; the permanent magnet frequency conversion screw machine can start and stop unlimited times, and only one pressure point is enough. For every saving of 0.14bar pressure difference, the system can save energy by 5~7%.
3. Save energy consumption during start-up
The starting current of the screw machine is 3-6 times of the rated current, and frequent starting will consume a lot of electricity; the permanent magnet variable frequency screw machine starts with a soft start, and the maximum current does not exceed the rated current.
At present, the energy consumption of air compressors is huge, and up to 70% of the electricity bills of general factories come from the consumption of air compressors. In contrast, what are the advantages of permanent magnet variable frequency screw air compressors?
Energy efficiency rating:
Assuming that the calculation is based on the model with a rated power of 37kW, the speed is the same as 3660rpm, the exhaust pressure is 0.8MPa, and the displacement Qo=5.84m⊃3;/min
a. The input power of the permanent magnet synchronous frequency conversion model is measured as Pi=40.36kW, then the input specific power of the whole machine is: qi=Pi/Qo=40.36/5.84=6.91
b. The input power of the ordinary asynchronous power frequency model is measured as Pi=43.64kW, and the input specific power of the whole machine is: qi=Pi/Qo=43.64/5.84=7.47
According to the standards of screw air compressors in “GB15193-2009 Positive Displacement Air Compressor Energy Efficiency Limits and Energy Efficiency Grades”, the first-level energy efficiency is the input specific power qi<7.2, and the second-level energy efficiency is the input specific power 7.2≤qi<8.1, so The permanent magnet synchronous model has a first-level energy efficiency, and the ordinary asynchronous power frequency model can only achieve a second-level energy efficiency.
Better volume regulation:
In order to achieve a balance between the exhaust volume of the air compressor and the air consumption of the user, the commonly used air volume adjustment methods for ordinary air compressors are intake throttling adjustment, loading/unloading adjustment, etc. Due to the existence of intake throttling, the vacuum is too large , and pressure loss during loading and unloading, etc., the energy saving effect of these methods is not ideal.
Later, due to the development of motor frequency conversion control technology, an adjustment method by controlling the motor speed appeared. This method can make the power consumption and exhaust volume of the air compressor change in a linear ratio, and it is gradually becoming popular. But this control method has the following defects:
1. When the speed and load of ordinary asynchronous motors are lower than the design rated point, the efficiency of the motor will drop significantly, and the greater the difference, the more obvious the drop in efficiency
2. When the ordinary asynchronous motor runs at a lower frequency, there will be a problem of insufficient output torque, which will cause the inverter to trip due to “motor torque overload”
3. Ordinary asynchronous motors will also experience unstable speed, increased vibration and noise, and increased heat generation when running at a lower frequency. Even if the current vector control method is adopted, the above shortcomings cannot be completely eliminated.
The current new control method is the control method of permanent magnet motor + special variable frequency drive, which has high efficiency and can always be maintained at a high level, constant torque operation at any speed, stable speed, and fast response to speed changes ( The acceleration time from 0 to rated speed is within 50ms, and there is no inrush current), low noise and other advantages.
Excellent energy saving:
Also according to the above two models with a rated power of 37kW, when the load rate is only 60%, the input power of the industrial frequency model controlled by ordinary air intake throttle is 38.2kW, while the shaft power of the permanent magnet variable frequency model is 23.6 kW, the power saving rate reaches 37.5%.
If calculated on the basis of 4,000 hours of work per year, the annual electricity cost of the ordinary asynchronous power frequency model is 107,200 yuan, and if the permanent magnet synchronous frequency conversion model is used, the annual electricity cost is 65,800 yuan. The electricity bill is 41,400 yuan.
Sollant Focus on Energy Saving