Thermal management of screw air compressor in high power laser cutting machine
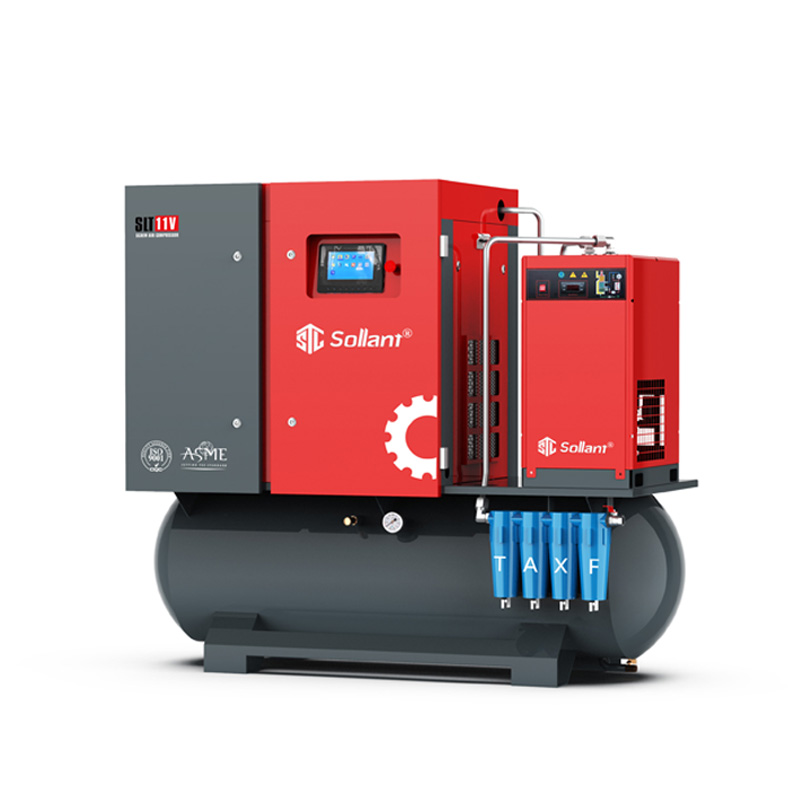
In high-power laser cutting machines, the thermal management of the screw air compressor is very critical. Since laser cutters require a lot of compressed air to maintain cut quality and speed, screw air compressors generate a lot of heat. If left untreated, this heat can cause the screw air compressor to overheat and even damage the unit. Therefore, effective thermal management is required to protect screw air compressors and laser cutting machines.
The following are some commonly used screw air compressor thermal management methods:
Cooling system: Screw air compressors are usually equipped with a built-in cooling system, which can control the temperature by circulating cooling water or oil. This cooling system can effectively reduce the temperature of the screw air compressor, thereby protecting the equipment.
Air cooling: In addition to the built-in cooling system, the screw air compressor can also use the air cooling system to control the temperature. This method can be achieved by passing air through the screw air compressor to absorb its heat and expel it.
Heat exchanger: The heat exchanger can be used to transfer the heat generated by the screw air compressor to other equipment or systems, thereby reducing the temperature of the screw air compressor. This approach increases overall system efficiency and reduces energy waste.
Temperature monitoring and alarm system: The temperature monitoring and alarm system can monitor the temperature of the screw air compressor in time and send out an alarm when it reaches the preset threshold. This ensures timely action to avoid equipment damage due to overheating.
To sum up, thermal management is very important for screw air compressors in high-power laser cutting machines. By using methods such as built-in cooling system, air cooling system, heat exchanger, and temperature monitoring and alarm system, the temperature of the screw air compressor can be effectively controlled to prevent equipment damage and improve the efficiency of the entire system.
Sollant Focus on Energy Saving