Why does the exhaust volume decrease after air compressor maintenance?
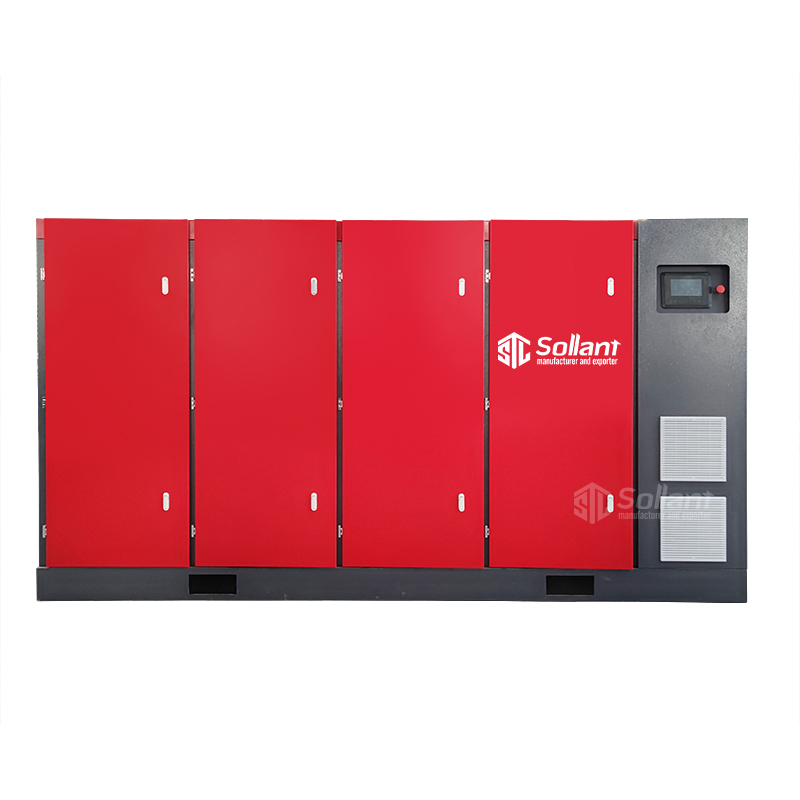
When an air compressor fails and is repaired, a situation sometimes occurs. The air compressor is obviously repaired, but the displacement has dropped. Could it be that the air compressor has a new failure? Don’t worry, in this article, the editor will help you understand why the air compressor malfunctions and the exhaust volume decreases after being repaired.
- Common faults and solutions of air compressors
The screw compressor is a positive displacement compressor, which is composed of a driving rotor and a driven rotor that mesh with each other, a body and a pair of synchronous gears. Therefore, common faults of screw compressors are as follows:
(1) The bearing is burned out. Foreign matter entering the oil system, oil pressure reduction, oil quality deterioration and other reasons may cause bearing burnout. The main treatment methods are: check the oil supply system; clean the oil filter and oil cooler cooling pipe; check and adjust the oil pressure regulating valve; test the oil quality and change the oil if the quality is not good; check and deal with oil leakage points.
(2) The rotor is burned out. Foreign matter enters the compressed medium system, or the rotor temperature rises due to high suction medium temperature, increased compression ratio, etc., the temperature of the rotor cooling oil rises, poor assembly of parts, deformation of the shell, etc. can cause the rotor to burn out. The main treatment methods are: check the air system; clean the intercooler; check the cooling water volume of the cooler and water jacket; clean the oil cooler; check the nozzles and channels of the oil cooler.
(3) Abnormal vibration sound. Vibration and abnormal sound are caused by shaft shaking or poor shaft joint. Treatment methods often require disassembly and inspection.
- Why does the exhaust volume decrease after the air compressor is repaired?
So why does the air volume sometimes decrease after the air compressor is overhauled? The main reasons are as follows:
Air compressor maintenance
(1) Incorrect maintenance and installation;
(2) If the maintenance and installation are correct, the main reason is that the air distribution mechanism (a complete device that controls the entry and discharge of air into the cylinder) and the piston components have not been run-in yet.
Any machine must go through a certain amount of running-in after installation before it can work properly. The same is true for air compressors. For an air compressor that has not been run-in after maintenance, its air distribution mechanism and piston components cannot be tightly matched. In this way, the suction resistance and gas leakage may be greater, and the air volume will naturally be smaller.
Sollant Focus on Energy Saving