How to Use Industrial Air Compressors: A Comprehensive Guide
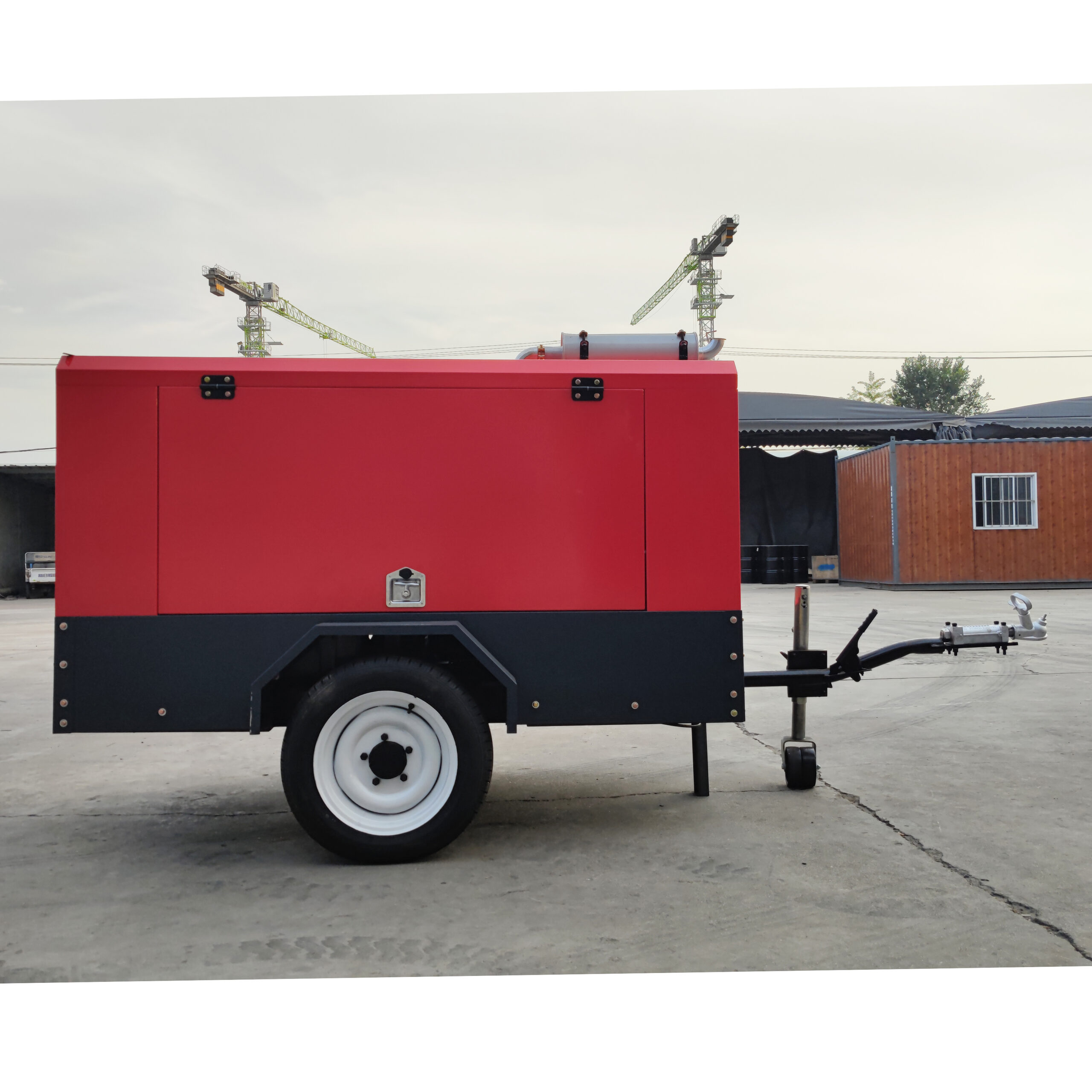
Introduction: Industrial air compressors are essential tools in various industries, from construction to manufacturing. They provide the power needed for heavy-duty equipment in locations where stationary compressors are impractical. Understanding how to use these mobile units efficiently can improve productivity, ensure safety, and prolong the lifespan of the equipment. This guide will walk you through the steps for using an industrial air compressor effectively.
1. Safety First: Inspect Before Use
Before starting the air compressor, perform a thorough inspection. Check for any visible damage to the machine, air hoses, and fittings. Ensure that all safety features, such as pressure relief valves, are in proper working order.
- Key Tip: Never operate the compressor if there are any signs of wear or damage. Faulty equipment can lead to accidents or equipment failure.
2. Set Up the Compressor Correctly
Position the mobile air compressor on a flat, stable surface. Ensure the machine is securely grounded to prevent vibrations or tipping. Mobile air compressors often come with wheels, but stabilizing the machine before use is essential for safe operation.
- Note: Avoid positioning the compressor near flammable materials or in poorly ventilated areas. Proper ventilation is crucial to prevent overheating.
3. Connect the Hoses and Tools
Once the compressor is in place, connect the appropriate air hoses to the outlet valve. Ensure the connections are tight to prevent air leaks. Afterward, attach your pneumatic tools to the hose.
- Key Tip: Always use the correct hose size and fittings for your application to ensure efficient airflow and performance.
4. Check the Oil Level
If you’re using an oil-lubricated compressor, check the oil levels before starting the machine. Proper lubrication is critical for the smooth operation of internal components and to avoid wear and tear.
- Note: Always use the recommended oil type specified by the manufacturer. Overfilling or underfilling the oil can damage the compressor.
5. Power On and Adjust Pressure
Turn on the air compressor and let it build pressure to the required level. Most mobile air compressors have an adjustable pressure regulator that allows you to control the output based on the tools you’re using.
- Important: Always start with the lowest pressure setting and gradually increase it to the required level. Over-pressurizing can damage the equipment or cause safety hazards.
6. Operate the Compressor Safely
While the compressor is running, keep an eye on the pressure gauge to ensure it remains within safe operating limits. Do not leave the machine unattended while it’s in use. If you’re working with multiple tools, be aware of the compressor’s capacity to avoid overloading.
- Key Tip: Regularly release the air pressure when switching tools or taking breaks to avoid excessive wear on the compressor and hoses.
7. Shut Down and Maintenance
After completing your work, turn off the compressor and release the pressure by opening the drain valve. Properly disconnect all hoses and store them neatly. Regular maintenance is crucial to prolong the life of the machine. Clean or replace the air filters, check for oil leaks, and inspect belts and fittings regularly.
Using an industrial air compressor effectively requires careful attention to setup, safety, and maintenance. By following these steps, you can ensure that your equipment operates efficiently and safely, leading to better productivity and longevity. Make sure to consult the manufacturer’s manual for specific instructions regarding your compressor model.