Principles of various air compressors-piston machine-screw machine-sliding vane machine
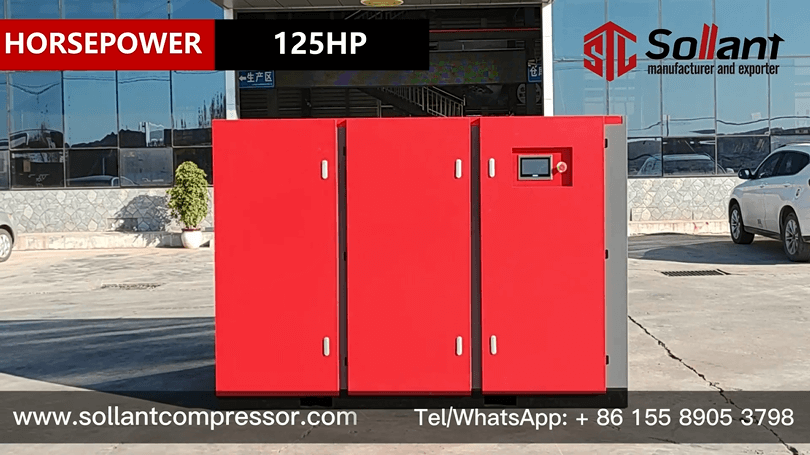
1. Piston type air compressor, this kind of air compressor has the earliest history, and it is also the air compressor with the highest working efficiency and the lowest commercial cost so far. Speaking of which, everyone can think about it carefully. All the inventions created by human beings for the first time in our history are often of the greatest value, and they are irreplaceable in a long history. For example, our bicycles , no matter how you change it, most of the bikes that stay with us are the original principles. The same goes for the air compressor.
2. Sliding vane air compressor, also known as rotary vane air compressor, is a continuous exhaust air compressor. Its rotor is the only part that runs continuously. There are several slots cut along the length of the rotor. A sliding piece that can slide on the oil film is inserted in it. The rotor rotates in the stator of the cylinder. During rotation, centrifugal force throws the vanes out of their grooves, creating individual compression chambers. The rotation makes the volume of the compression chamber decrease continuously and the air pressure increase continuously. Finally the high pressure air is exhausted from the exhaust port. There are not many places where this kind of air compressor is used, and the flow rate at the same speed is very large. Almost all of our cars now use this kind of air compressor. His advantages are low noise and small size. The main disadvantage is that it has high requirements on the quality of the incoming air, and slightly larger impurities will cause irreversible damage to the rotary vane.
3. Screw air compressors are divided into single-screw and twin-screw. The helical rotor groove inside the air compressor is filled with gas when it passes through the suction port. When the rotor rotates, the rotor groove is closed by the casing wall to form a compression chamber. When the rotor groove is closed, lubricating oil is sprayed into the compression chamber to form a seal. Cooling and lubrication. When the rotor rotates to compress lubricant and gas, the volume of the compression chamber decreases, and the oil-air mixture is compressed to the exhaust port. When the compression chamber passes through the exhaust port, the oil-air mixture is discharged from the compressor, completing a suction-compression-exhaust process.
Sollant Group-Professional Compressed Gas Solutions Provider