Transmission mode of screw air compressor —Shared by Sollant
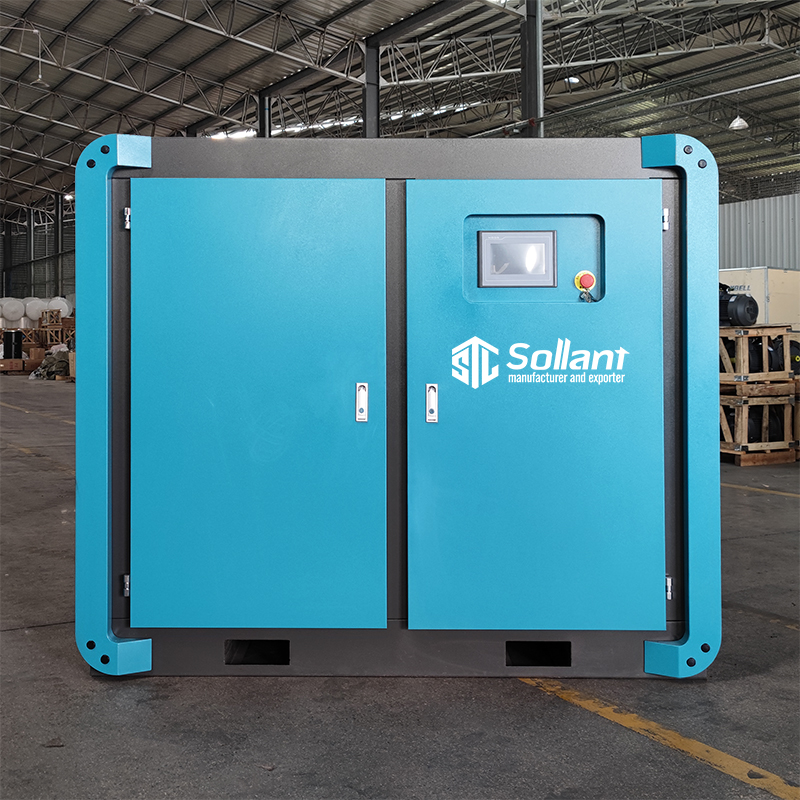
Screw air compressor gear drive and belt drive, in the drive system of screw air compressor, can generally be divided into direct drive and belt drive. For a long time, the advantages and disadvantages of these two transmission methods have been one of the focuses of debate in the industry.
The direct drive of the screw air compressor means that the motor shaft drives the rotor through the coupling and the gearbox, which is not actually a direct drive in the sense. Direct drive in the sense means that the motor is directly connected (coaxially) to the rotor, both at the same speed. This is obviously very rare. Therefore, the statement that there is no energy loss in direct transmission is not true.
Another type of transmission is the belt drive, which can vary the speed of the rotor by using pulleys of different diameters. The belt transmission system discussed below is an automated system, which represents the current technical level and meets the following conditions: the belt tension reaches an optimal value in each operating state, and by avoiding excessive starting tension, the working life of the belt is greatly extended, and the The load on the motor and rotor bearings is reduced; the correct pulley connection is always ensured; the replacement of the belt is quite simple and quick, no adjustments to the original settings are required; the entire belt drive system runs trouble-free. Compared with screw air compressor gear drive and belt drive, no-load energy consumption For spur gear drive, the no-load pressure is generally kept above 2.5bar, and some even as high as 4bar to ensure the lubrication of the gearbox.
For belt drive, theoretically, the no-load pressure can be zero, because the oil sucked into the rotor is enough to lubricate the rotor and bearings. The pressure is maintained at around 0.5 bar. Lost Oil Experienced real-world users know that in the event of an oil spill, the transmission suffers first. The belt drive does not have this problem.
The belt drive design manufacturer representing modern technology can design the working pressure to be consistent with the user’s needs only by changing the diameter of the pulley, so that the user can obtain more air volume under the same motor power. With wheel drive, you don’t get the same convenience. The pressure of the installed screw air compressor changes. Sometimes due to the change of the customer’s production process conditions, the original design pressure of the purchased air compressor may be too high or too low. I hope it can be changed, but for the gear-driven air compressor, this work is very important. Difficult and expensive, but easy for belt drive air compressors, just replace the pulley.
Replacing the shaft seal Any screw air compressor uses an annular shaft seal, which needs to be replaced until a certain lifespan. For gear transmission air compressors, the motor and coupling must be separated before access to the shaft seal, which makes the work time-consuming and laborious, thereby increasing maintenance costs.